Hinter den Kulissen: „Guck nicht, wofür du zuständig bist. Guck, was Du machen kannst.“
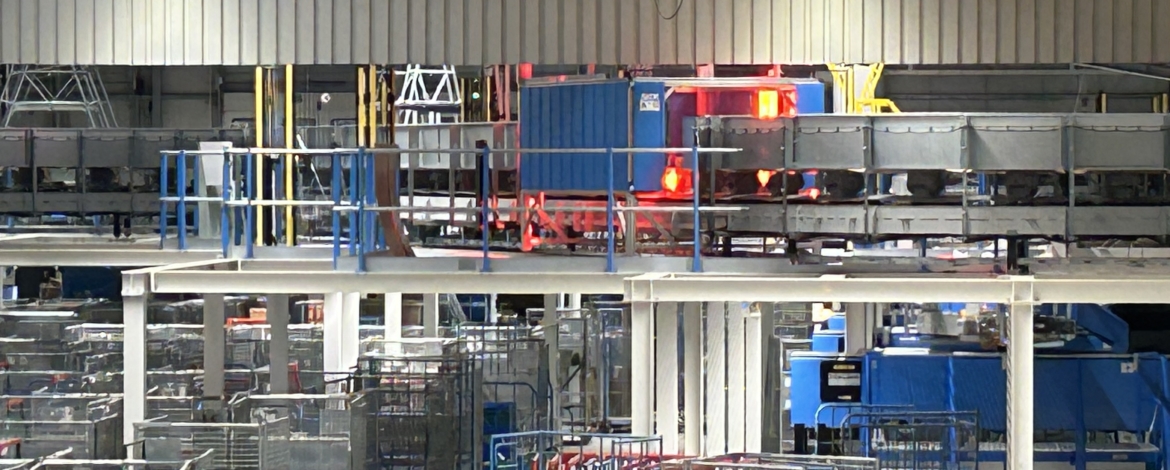
Das Freiburger Depot von Hermes Germany. (Foto: Hermes Germany)
Die Mail aus der Real Estate Abteilung ließ keine Fragen offen: „Wir treffen uns morgen um sechs Uhr. Mit Schaufeln, Gummistiefeln und warmer Kleidung, die dreckig werden kann.“ Das Ziel: Gemeinsam mit seinem Team wollte Kai Reinelt, der Manager des Depots von Hermes Germany in Freiburg, einen 50 Meter langen Kabelkanal graben, um die gerade installierte neue Förderanlage mit einem Stromverteiler zu verbinden. Denn keiner der Dienstleister, die an dem monatelang dauernden Umbau beteiligt waren, fühlte sich dafür zuständig. „Man hätte lange herumdiskutieren können, wer dafür nun die Verantwortung trägt“, sagt Reinelt und grinst. „Oder man schnappt sich eine Schaufel. Mein Motto ist: Guck nicht, wofür du zuständig bist, sondern guck, was Du machen kannst.“
Pragmatische Lösungen finden, anpacken statt diskutieren – deshalb hat Reinelt Speditionskaufmann gelernt. „Der Job ist anders als in anderen kaufmännischen Berufen“, sagt er: „In der Logistik sitzt man nicht den ganzen Tag am Schreibtisch, sondern ist auch in der Halle oder auf dem Hof unterwegs. Man hat viel mit Technik zu tun, mit Maschinen und Fahrzeugen – und natürlich mit Menschen.“
30 Jahre Verbundenheit mit Hermes Germany
1995 kam Reinelt zur heutigen Hermes Germany – und blieb. „Weil ich immer das Gefühl hatte, fair behandelt zu werden. Man spürt immer noch das Familienunternehmen Otto“, sagt er. „Ich konnte immer auf das Vertrauen meiner Vorgesetzen zählen.“
2006 wird Reinelt Disponent im Freiburger Depot, das er heute leitet. Einige Jahre später steht der Standort mit Blick auf gestiegene Anforderungen auf dem Prüfstand. Die zentralen Fragen waren: Wie geht es weiter und wie können wir den Standort, auch für alle Mitarbeitenden, wieder voranbringen? „Gemeinsam haben wir vor Ort an einem Strang gezogen. Und ich kann sagen: Es hat sich gelohnt!“ sagt Reinelt.
Veraltete Technik vs. steigende Anforderungen
Spätestens jetzt ist das Depot für Reinelt mehr als ein Arbeitsplatz. Seine Arbeitszeiten legt er so, dass sie sich mit den Schichten der Lagermitarbeitenden überschneiden. Regelmäßig geht er durch die Halle und tauscht sich mit den Fahrer*innen aus, die an der hauseigenen Kaffeebar noch einen kostenlosen Kaffee trinken. Und er überlegt ständig, wie sich hier, an einem der ältesten Depots von Hermes Germany, Prozesse effizienter gestalten lassen. Auch wenn das immer schwieriger wurde.
„Die Eingangsmengen wurden immer größer, die Zeitfenster für den Umschlag immer kürzer und die Anlieferungszeiten immer später, sogar um 23 Uhr wurden noch Pakete geliefert“, erzählt Reinelt. „Das kann man mit 25 Jahre alter Technik nicht bewältigen. Der steigende Druck wurde zur Belastung. Es war klar: Wenn wir unsere Ziele noch erreichen wollen, müssen wir investieren.“
Monatelang planten Kai Reinelt und sein Team 2024 die Modernisierung. Das Herz: ein maßgeschneidertes Loop-Sorterkonzept. Der Umbau bei laufendem Betrieb brachte mehr als eine Herausforderung. So, wie es Reinelt mag. Beispiel gefällig? „Kurz vor der Installation rief der Maschinenbauer an, weil er Gutachten über die Tragfähigkeit des Bodens brauchte“, erinnert er sich: „Sonst könnten wir nicht aufbauen.“
Hiobsbotschaft? Ansporn!
Doch das geforderte Dokument war unauffindbar – und das ganze Projekt stand plötzlich auf der Kippe. Doch was wie eine Hiobsbotschaft klingt, war für Reinelt und seine Kolleg*innen ein Ansporn: „Ich überlegte: Wer könnte so etwas erstellen? Er googelte, fand einen renommierten Geologen, rief ihn an und bekam die Bestätigung: „Ja, so etwas könnte ich machen.“ In etwa sechs Wochen habe er Zeit, fügte der Experte noch hinzu. Reinelt muss lachen, als er die Geschichte erzählt: „Ich sagte: Tut mir leid, aber Sie müssten morgen früh um sieben Uhr hier sein.“ Tatsächlich war am nächsten Morgen der Experte vor Ort, entnahm Bodenproben und erstellte ein Gutachten, das bestätigte: Die Maschine kann gebaut werden. „Regeln sind wie Leitplanken“, meint Reinelt dazu: „Sie begrenzen einen nach rechts und links, aber wie schnell man geradeaus fährt und auf welcher Spur – das hat jeder selbst in der Hand.“
Mehr Effizienz, weniger Belastungen für die Mitarbeitenden
Der Einsatz hat sich gelohnt. Das kann Reinelt sogar hören. „Bei den alten Maschinen war jedes Lager eingelaufen“, sagt er: „Die Geräuschkulisse war hoch. Heute ist alles viel leiser.“ Auch die körperliche Belastung wurde reduziert. Die Laufwege sind jetzt kürzer, die Förderbänder höher und damit rückenfreundlicher, große Pakete werden mit niedrigerer Geschwindigkeit transportiert, sodass sie leichter angehoben werden können.
Neue Klapprutschen und ebenerdige Beladungsmöglichkeiten für die LKW sorgten gleichzeitig dafür, dass sich die Umschlagmengen enorm erhöhten. Die Zahl der täglich abgewickelten Sendungen steigerte sich um fast 30 Prozent auf heute im Schnitt rund 23.000. Davon werden täglich ca. 10.000 vor Ort in Transporter verladen. Dieser Prozess benötigt rund anderthalb Stunden. „Wir wollten die Effizienz steigern“, bilanziert Reinelt. „Dass das dank der starken Teamleistung so gut geklappt hat, macht mich ein bisschen stolz.“ Dafür schaufelt man auch gern mal bei strömendem Regen einen Kabelkanal.